Tectonic Dusts

Stone sludge. SE, 2023.
Tectonic Dusts is an exploration into the residual by-products resulting from stone quarrying and processing in Vals, Switzerland, with a particular focus on quartzite. The journey of stone, from quarry to final product, involves numerous processing steps, each contributing to the volume of discarded material. While some offcuts could potentially be repurposed and are not environmentally detrimental when landfilled, a significant portion of the waste consists of cutting and grinding dust. This dust, characterised by its fine granularity and potential contamination, requires specialised handling.
In this initiative, we propose an approach to repurpose stone processing waste into building materials, ranging from bricks to tiles. Inspired by the natural rock cycle, production process involves pressing and firing the material. This project is as much about practical solutions as it is about changing perceptions, demonstrating the hidden potential in what is traditionally seen as waste.
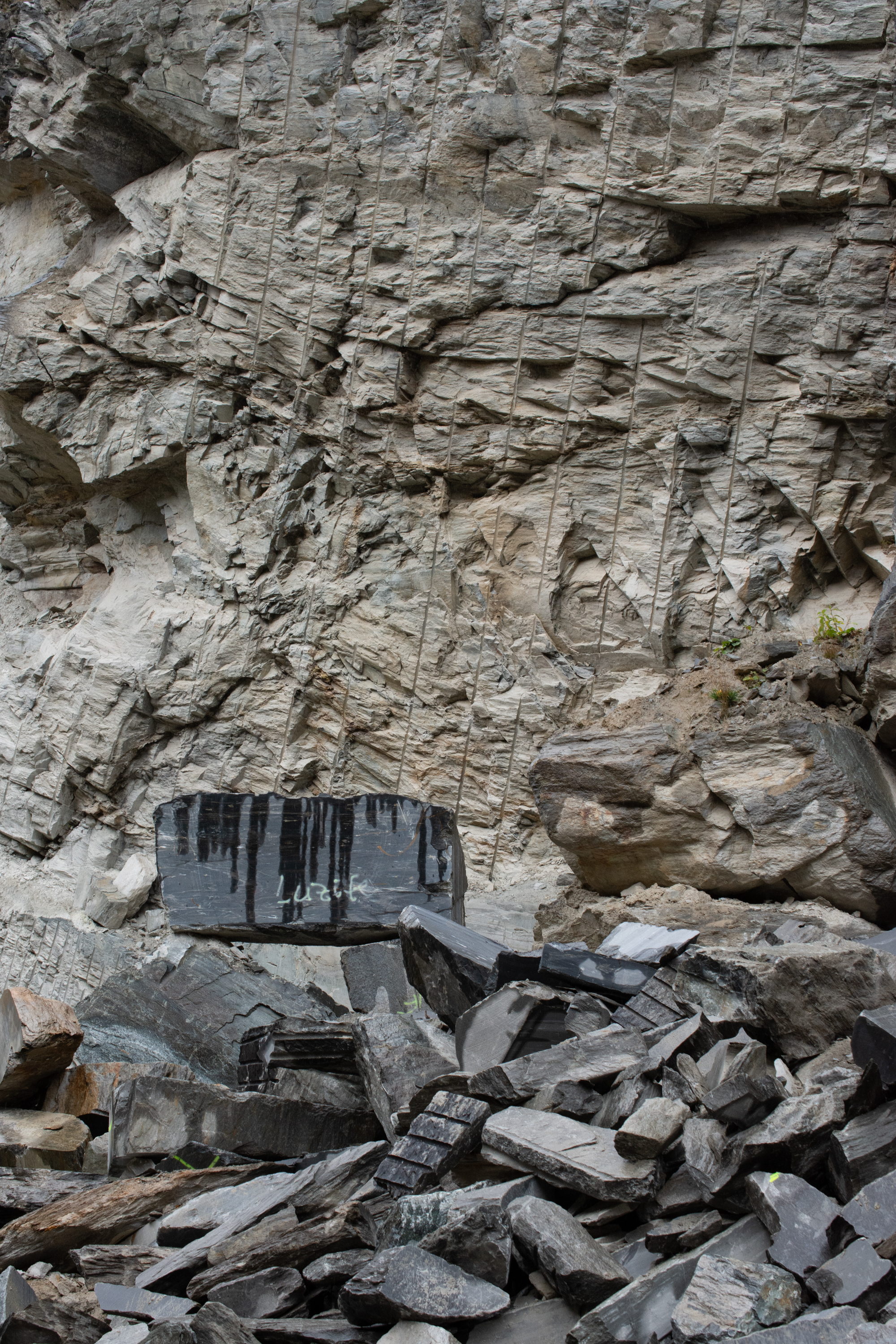

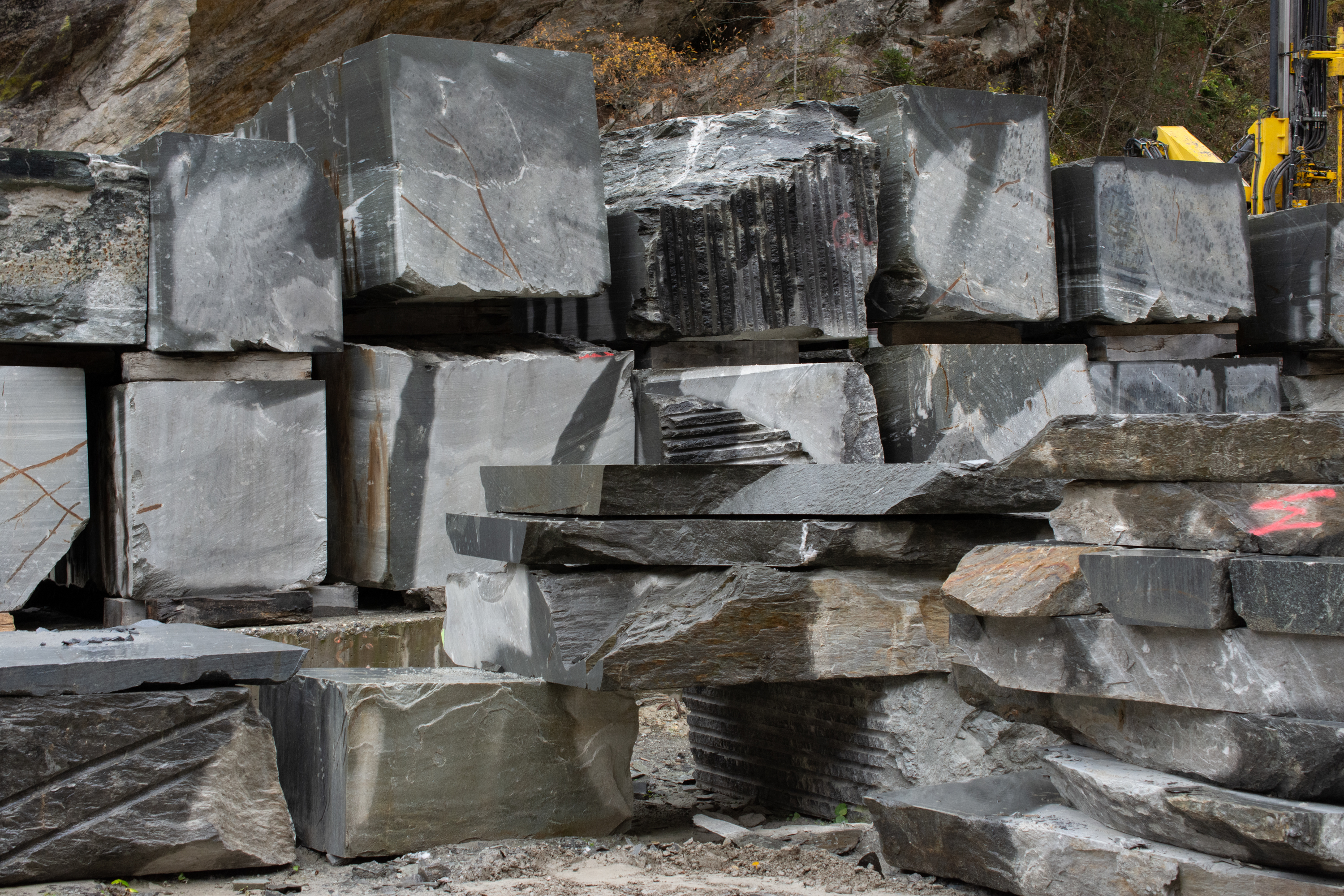
Stone blocks after the extraction. SE, 2023.

Stone cutting with diamond blade. SE, 2023.



Stone sludge, also referred to as stone slurry, emerges as a significant byproduct of the natural stone processing
industry. During the quarrying and processing phases, up to 35% of the extracted stone volume is converted into waste, broadly categorized into solid stone scraps and
stone sludge. This sludge, with a consistency akin to silky clay, poses environmental challenges due to its fine grains and contamination with heavy metals like nickel and cobalt,
a consequence of using diamond blades in the cutting
process.
The production of stone sludge is largely attributed to the stone cutting process, where water is used both as a cooling agent and as a means to remove fine stone particles from beneath the cutting tools. This process creates a mixture of ground rock mass, water, and occasionally, small quantities of abrasive material from synthetic diamonds. The granular composition of stone sludge is predominantly finer than 100 microns, making it a substantial contributor toprocessing-related waste. With the global volume of natural stone traded in 2018 amounting to 83.4 million tonnes, the management and utilization of stone sludge become increasingly relevant.
The production of stone sludge is largely attributed to the stone cutting process, where water is used both as a cooling agent and as a means to remove fine stone particles from beneath the cutting tools. This process creates a mixture of ground rock mass, water, and occasionally, small quantities of abrasive material from synthetic diamonds. The granular composition of stone sludge is predominantly finer than 100 microns, making it a substantial contributor toprocessing-related waste. With the global volume of natural stone traded in 2018 amounting to 83.4 million tonnes, the management and utilization of stone sludge become increasingly relevant.
The management of stone sludge involves a meticulous process to mitigate its environmental impact. Once generated, the sludge is collected, and the water content is substantially reduced using filter presses. This step is crucial as it transforms the sludge from a fluid state to a more manageable solid form. The concentrated sludge is
then transported by truck to designated municipal landfill sites. At these sites, the sludge is stored on specific areas with concrete flooring. This containment strategy is essential to prevent the leached contaminants, from mixing with natural water sources and soil. If not properly managed, the fine particles and heavy metal contaminants can pose
significant environmental risks.
Studies highlight the benefits of efficient stone waste management, including potential revenue from selling stone waste, rational use of natural resources, reduced material loss in extraction and processing, and lower costs associated with waste storage, transportation, and disposal. This approach also enhances the social responsibility profile of companies in the industry.
Studies highlight the benefits of efficient stone waste management, including potential revenue from selling stone waste, rational use of natural resources, reduced material loss in extraction and processing, and lower costs associated with waste storage, transportation, and disposal. This approach also enhances the social responsibility profile of companies in the industry.


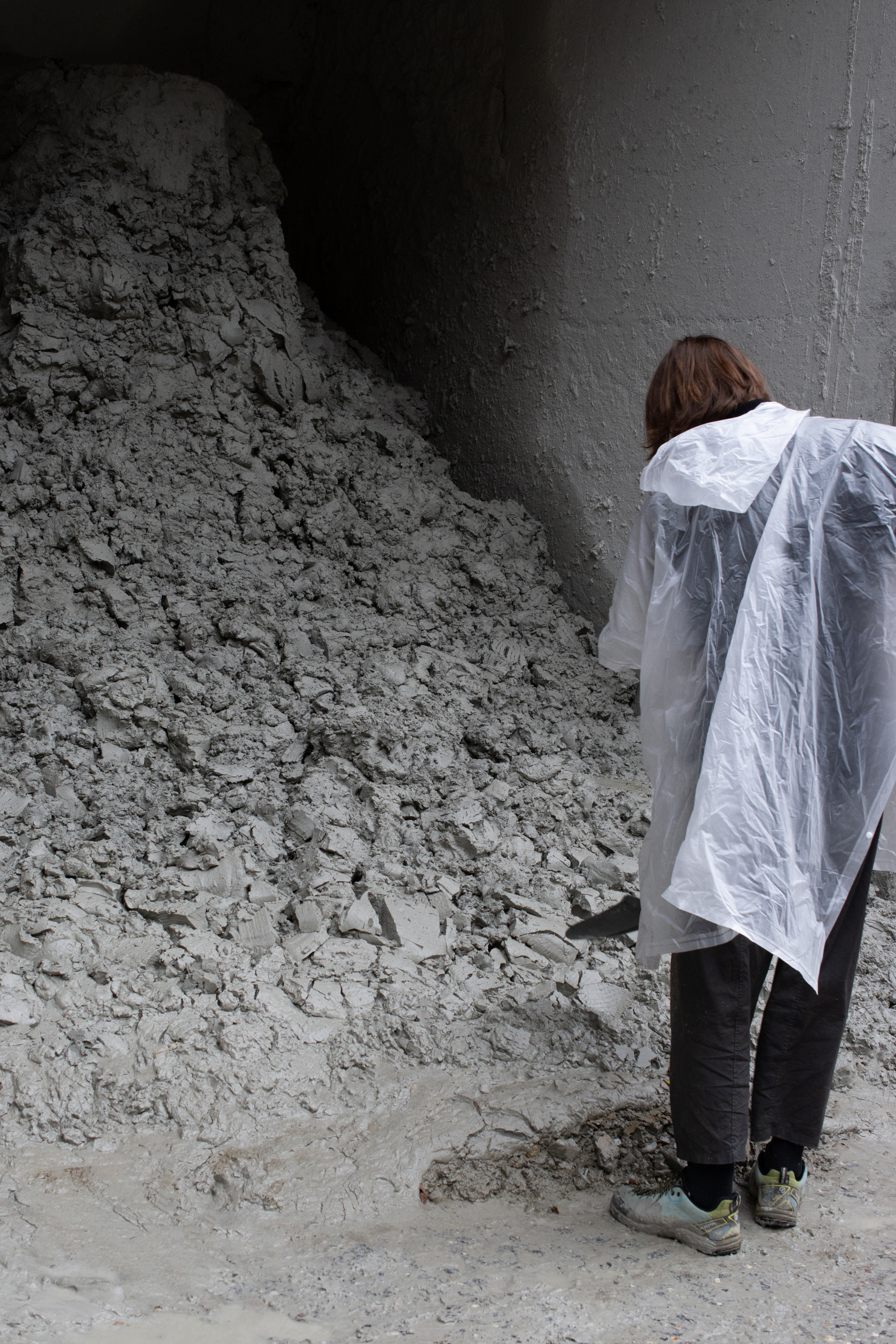

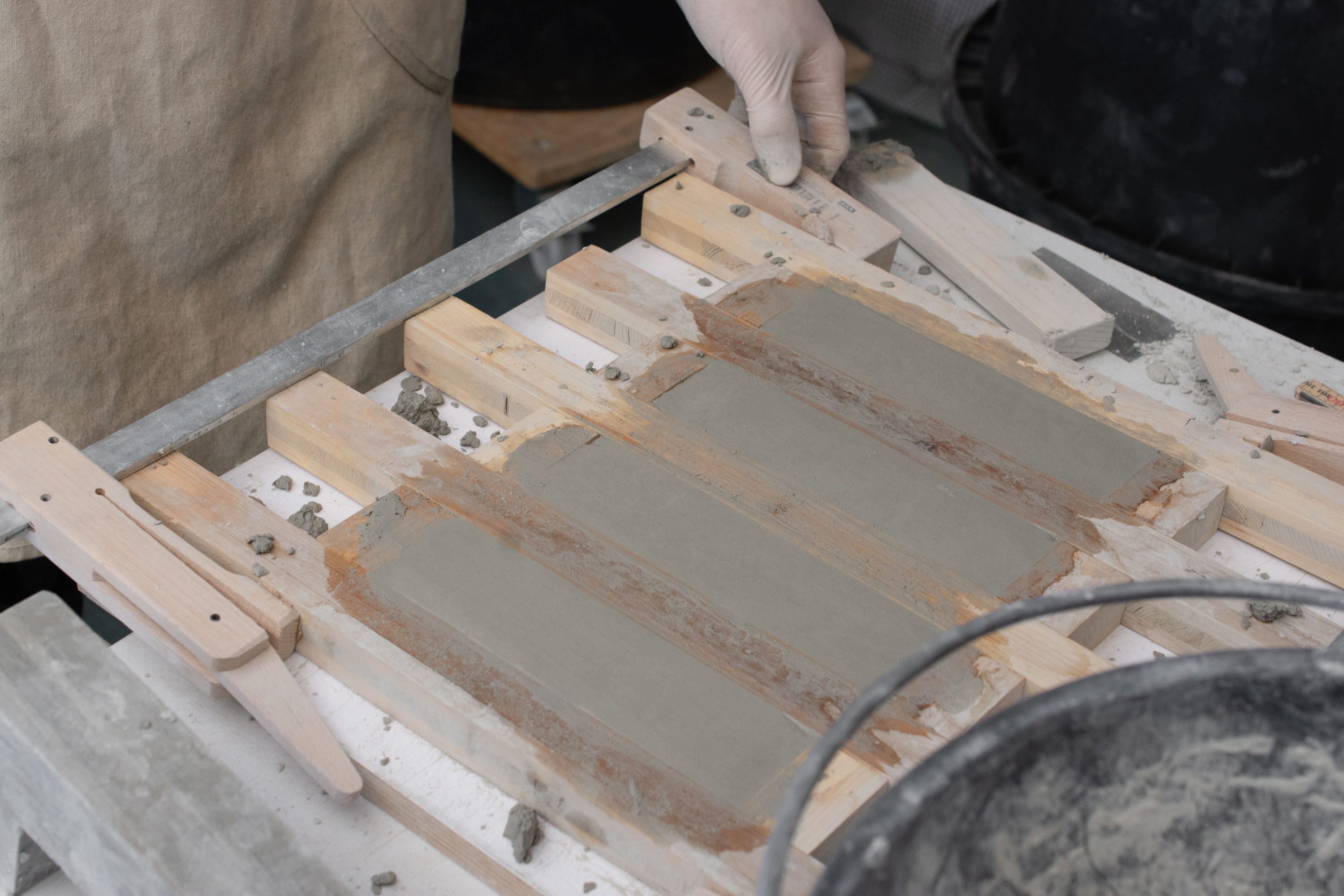
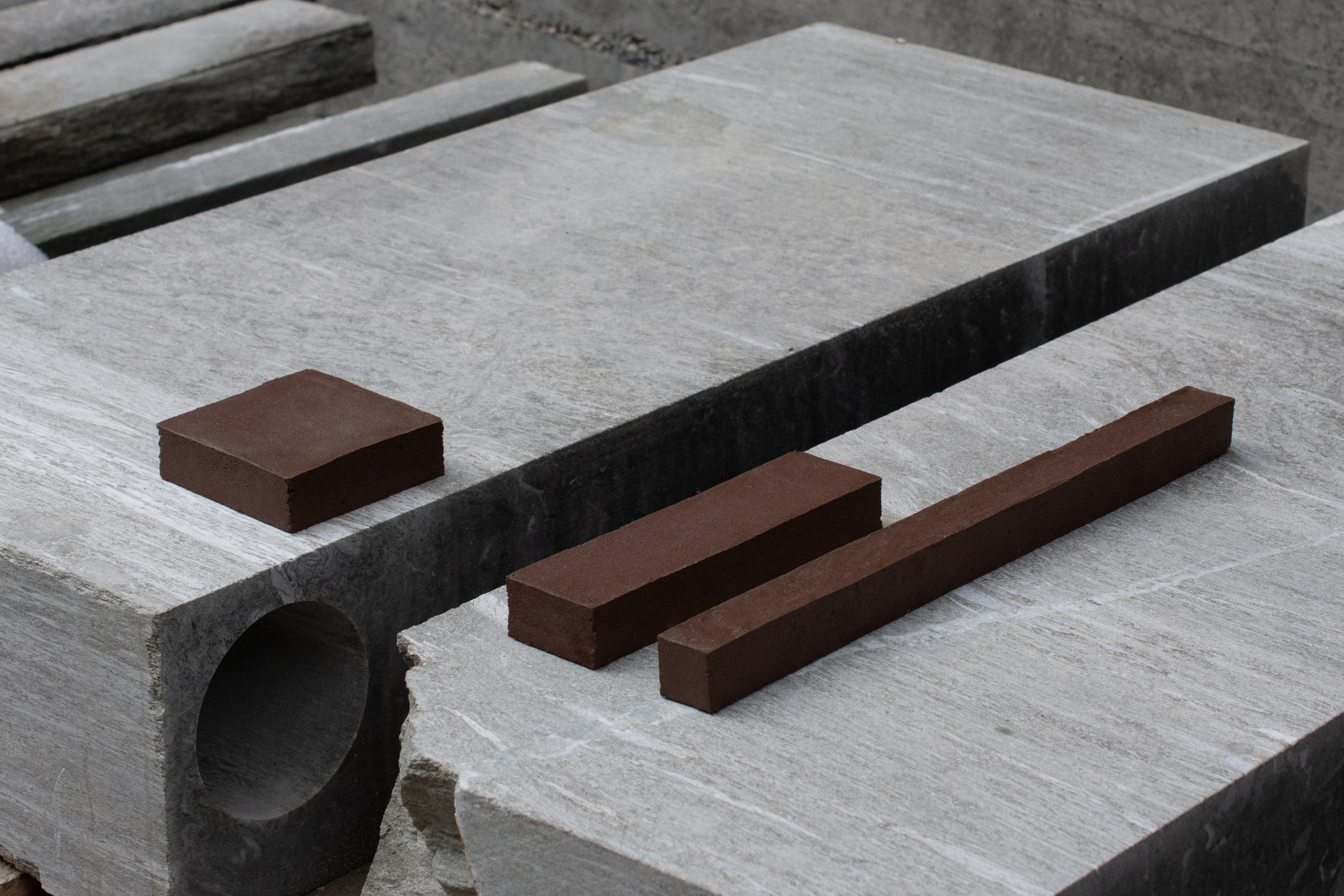
Three proposed formats of bricks. SE, 2024.

Color gradient in different firing temperatutes. SE, 2024.
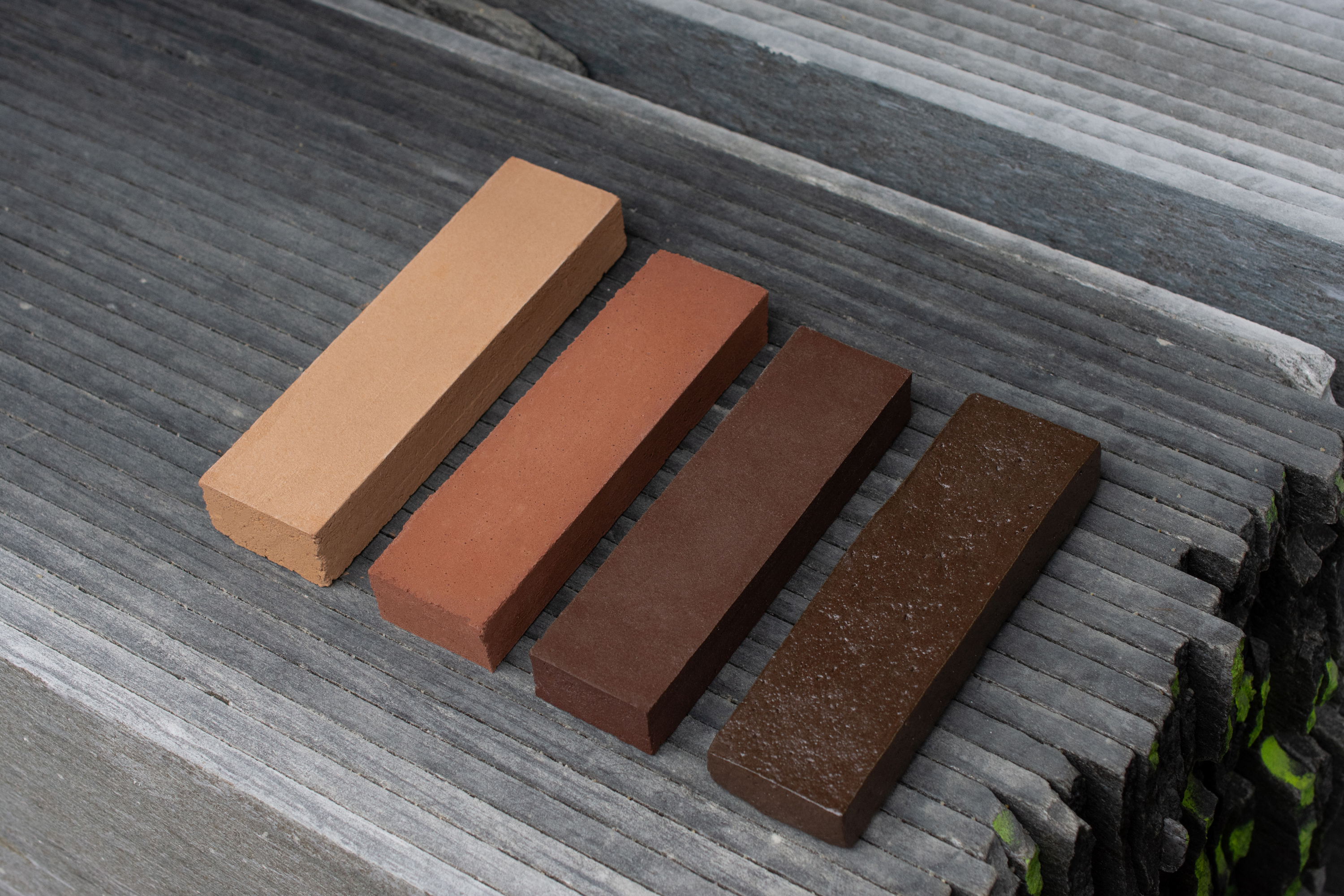


Stacking pattern. SE, 2024.

An abstract roof tiling installation. SE, 2024.



Stacking process. SE, 2024.
Project info
2023 - Vals -Graubünden - CH
Stone processing waste, as known as stone sludge.
Many thanks to Pia Truffer and Turffer AG for the support.
Contact us for more information about the research.